From Design to Complete: The Full Aluminum Spreading Refine Demystified
In the realm of manufacturing, the process of aluminum casting stands as a critical approach that has fueled sectors for decades. Stay tuned as we dissect the total light weight aluminum casting process, uncovering the complexities that change raw products right into polished products.
Designing the Casting Mold
When starting the light weight aluminum spreading process, meticulous attention to creating the spreading mold and mildew is extremely important for ensuring the end product's integrity and quality. The spreading mold acts as the structure for the entire casting procedure, dictating the form, dimensions, and surface finish of the eventual aluminum component.
To develop an effective spreading mold and mildew, engineers must think about various variables such as the complexity of the component, the sort of aluminum alloy being used, and the desired homes of the end product. about aluminum casting. Computer-aided layout (CAD) software application is usually utilized to develop in-depth schematics of the mold, enabling specific personalization and optimization
In addition, the design of the casting mold and mildew straight influences the performance and cost-effectiveness of the casting procedure. A properly designed mold and mildew minimizes material waste, lowers the need for comprehensive post-casting machining, and boosts overall manufacturing rate.
Melting and Pouring Aluminum
With the layout of the casting mold and mildew settled, the following important step in the light weight aluminum spreading procedure is the melting and pouring of the aluminum alloy. As soon as the aluminum is molten, it is important to preserve the temperature within a particular variety to ensure the high quality of the spreadings.
After the aluminum gets to the desired consistency, it is time for pouring. The liquified aluminum is very carefully moved from the furnace to the casting mold and mildew. This action requires precision and control to prevent issues in the last product. The putting procedure has to be executed quickly to stop early solidification and ensure the aluminum loads the mold totally. Correct pouring strategies contribute dramatically to the total high quality of the last light weight aluminum casting.
Strengthening and Cooling Down Refine
Upon completion of the putting procedure, the liquified light weight aluminum shifts into the cooling and solidifying phase, a critical stage in the light weight aluminum casting procedure that straight impacts the final item's stability and characteristics. As the light weight aluminum begins to cool, its particles prepare themselves right into a solid form, gradually taking on the form of the mold and mildew.
During this phase, it is important to regulate the cooling procedure carefully to avoid flaws such as porosity, shrinking, or inner stresses. Various cooling approaches, such as air cooling, water quenching, or regulated cooling chambers, can be utilized based upon the particular needs of the spreading (about aluminum casting). By controling the solidification and monitoring and cooling procedure, producers can make sure the manufacturing of high-quality aluminum castings with the desired metallurgical and mechanical properties

Removing the Last Spreading
As soon as the light weight aluminum spreading has actually sufficiently solidified and cooled down in the mold and mildew, the next action in the procedure involves thoroughly getting rid Related Site of the final spreading. This step is essential to ensure that the light weight aluminum part is effectively drawn out with no damage or find out here problems.
To eliminate the casting, the mold and mildew is opened up, and the spreading is removed using various methods depending upon the complexity of the mold and the part design. For easier shapes, the casting can frequently be conveniently gotten rid of by hand or with straightforward devices. However, for even more complex layouts, extra tools such as ejector pins, air blasts, or hydraulic systems might be needed to promote the removal process without causing any injury to the casting.
After the casting is successfully removed from the mold, any kind of excess product such as gateways, joggers, or risers that were utilized during the spreading process are trimmed off. This step aids in accomplishing the last desired shape of the light weight aluminum part before it goes through any type of extra completing procedures.
Finishing and Quality Inspection
The last stage in the aluminum casting process involves meticulous finishing techniques and extensive top quality evaluation protocols to ensure the honesty and precision of the cast light weight aluminum components. Finishing techniques such as grinding, fining sand, and shot blasting are utilized to remove any excess product, smooth rough surface areas, and enhance the aesthetic allure of the end product. These processes not just improve the look yet likewise make certain that the components meet the specified dimensional tolerances and surface finish demands.
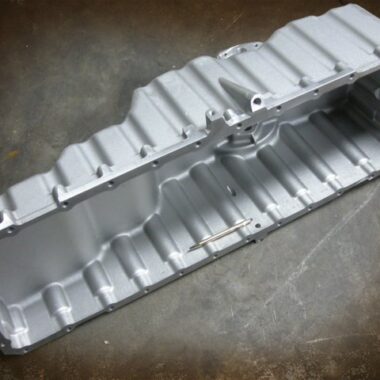
Verdict
To conclude, the light weight aluminum spreading process involves developing the mold and mildew, melting and pouring light weight aluminum, strengthening and cooling the spreading, getting rid of the end product, and do with a top quality evaluation. Each action is important in making sure the end product satisfies the wanted requirements. By understanding the entire process, manufacturers can create high-grade light weight aluminum spreadings effectively and efficiently.
Keep tuned as we explore the full aluminum spreading process, revealing the details that change raw products into polished items.
With the design of the casting mold and mildew completed, the next vital step in the aluminum casting procedure is the websites melting and putting of the aluminum alloy.Upon completion of the pouring process, the liquified aluminum transitions right into the cooling down and strengthening stage, a crucial phase in the light weight aluminum casting procedure that straight influences the final item's honesty and attributes.The final phase in the light weight aluminum spreading process entails precise completing strategies and rigorous top quality assessment methods to make sure the integrity and accuracy of the cast light weight aluminum parts.In conclusion, the light weight aluminum casting procedure includes creating the mold, melting and pouring light weight aluminum, solidifying and cooling the spreading, removing the last product, and finishing with a high quality evaluation.